Vacuum Heat Treatment for 3D Printing: The Ultimate Guide
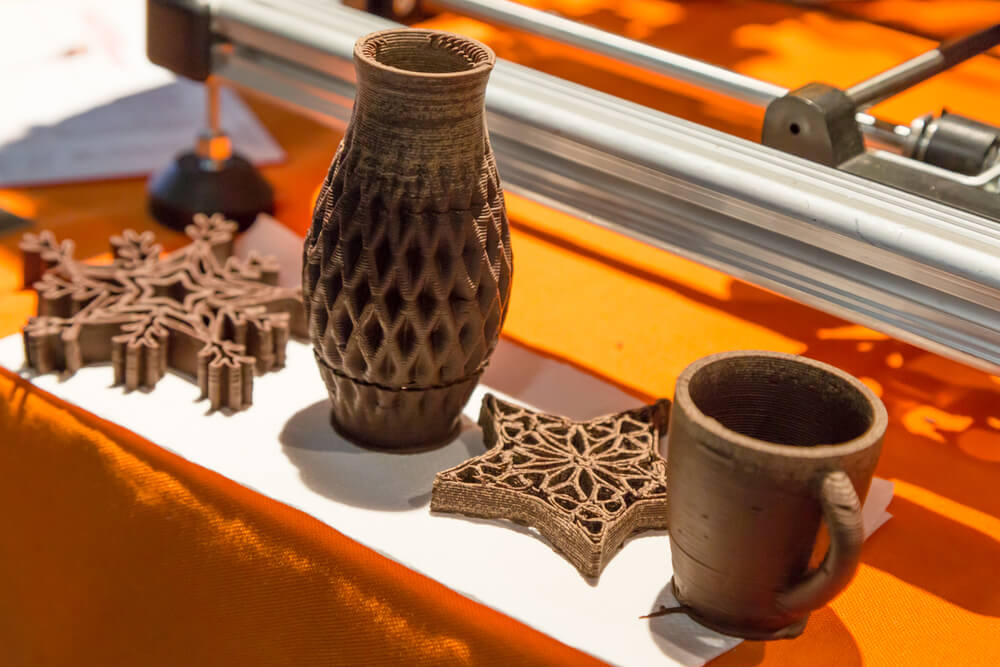
As technology advances, people discover different ways to do their tasks more efficiently than before, one of which is creating parts or components using 3D printing. This technology is quickly becoming more popular, especially in manufacturing metal products. It provides a faster production time and makes robust components for various applications.
However, not a lot of people know how it works. One of the essential processes involved in the entire 3D printing operation is vacuum heat treatment—one which you need to understand to optimize the characteristics of your metal products.
Here are some things you need to know about the 3D printing process before fully understanding the vacuum heat treatment’s role in the process.
How Does 3D Printing Work?
3D printing has been around since the 1980s, introduced as a method for creating plastic parts and prototypes cost-effectively. The process has evolved over the years and is now used to create different 3D objects in metals, ceramics, and plastic, making it an essential technology in various production environments. But how exactly does 3D printing work?
Also known as additive manufacturing, this process converts computer-aided design (CAD) models into metallic three-dimensional parts. The machine layers powders or feedstock into a shape close to the finished product or a dimensionally complete part. It’s different from subtractive manufacturing, where the 3D shape is carved from solid raw material, removing the excess to produce its size.
Metal printing with 3D technology prefers a powder bed fusion method where metal powder particles are fused point-by-point using a laser or electron beam. This creates the layering of the object, resulting in its final form.
The 3D Printing Process
Since 3D printing is complicated, the process follows a set of phases:
- Pre-Printing Phase
- Printing Phase
- Post-Printing Phase
1. Pre-Printing Phase
Before starting the printing phase, it’s essential to set up a conducive atmosphere surrounding your printing materials in all of the steps. For instance, oxidized powders from atomization processes in an ill-fitting environment can cause difficulty in melting or generating defects within the molded component’s materials.
This means you need to pay close attention to the production of the powders you’re going to use. After achieving the optimal levels for your powders, set the accretion chamber’s atmosphere to protect the process using inert gasses and prevent unwanted reactions.
However, there may still be small oxygen residue or impurities within the gas even with the inertization of the molten pool and chamber environment. This may result in pieces with unwanted colors and mechanical performance deterioration in the future. Therefore, you must follow the post-processing phase.
2. Printing Phase
Next up in your additive manufacturing process is the printing proper. There are different methods you can choose from, which may depend on what you’re working with.
Direct Metal Laser Sintering (DMLS)
This method may be the most prevalent as it can melt and fuse metal powders, catering to various materials. Unlike other techniques, DMLS can process materials such as titanium, Inconel, cobalt chrome alloys, and most metal alloys. It also produces metals free of residual stress and internal defects, which is important for parts operating under intense pressure.
DMLS uses a high-powered focus beam to create a molten base where metal powder is injected. Typically with a 400–1000-watt laser, the material’s surface is melted in a tightly controlled atmosphere, such as an inert chamber, to control oxidation. This creates a small molten base material pool where the powder is added to form a deposit.
The reusable build plate is spread with a layer of metal powder of about 0.1mm, which a laser will fuse. After this, a roller is used to create a new layer on top of the previous one. This will continue to fuse cross-sections or layers until the model is completed. Once the process is down, remove all loose or unfused powder from external surfaces, blind holes, cavities, and cooling passages.
Electron Beam Additive Manufacturing (EBAM)
Compared to the DMLS method, EBAM can process materials at a higher rate. It uses a multi-kilowatt electron gun inside a chamber of a vacuum oven. However, it does not produce a shape as fine as the other method.
Using a computer-controlled electron beam, the raw materials are preheated to melt and fuse wires or metal powders. Preheating reduces the need to reinforce the metal during manufacturing since it limits deformities. This process creates a dense 3D item directly from the raw materials with more support for the cantilever areas.
The EBAM method is commonly used to process materials like titanium 6AI-4V, other titanium alloys, and sometimes cobalt chrome. This technique can decrease the manufacturing time as it heats the powder simultaneously.
Binder Jet Process (BJP)
Out of the three methods of 3D printing, BJP is the most cost-effective as it works the same way as 2D paper printing, cutting down manufacturing time. It is also ten times cheaper than other 3D printing methods. The BJP method can produce high volumetric outputs.
However, it’s the most complicated to heat-treat using a vacuum furnace. This method typically processes raw materials like foundry sand, ceramics, metals, polymers, and composites. Its adherence to the principal concept of traditional 2D printing makes it work differently than DMLS and EBAM.
You will need two components for BJP: binder and powder. First, the raw materials or metallic powders are sprayed with the liquid binder, acting as an adhesive between the layers at ambient temperatures.
With the low heat source, the mix of binders and powders solidifies. The excess binders are often burned off or eliminated after printing within the confines of a special atmospheric furnace. However, there will still be a residue of binders, which evaporate from vacuum heat treatments.
When each layer solidifies, printed parts are lowered for the next until it completes the desired model.
One thing to note about this technique is that the vacuum furnace used will need to have a cold trap where unwanted binders are collected. Although this requires a specialized furnace, the payoff is worth it since it can make a range of colors and allows for a fast and large batch of processing for different binder-powder combinations or mechanical properties.
3. Post-Printing Phase
In additive manufacturing, the post-printing phase is the most important in optimizing the mechanical properties of the printed parts, especially for robust metals that need to withstand high amounts of pressure. Post-printing helps in achieving the required hardness, size, and density. Your printed metals will need to undergo heat treatment processes to do this.
One of the most common processes used is de-tensioning, which releases accumulated internal tensions in a material acquired from the printing phase. There are other types of processes optimizing the mechanical properties of a component specifically for its use.
These treatments are often done in a controlled condition or out in the air. Without the meticulous treatment of heat sintering, your printing products can result in faulty components or ones that may need significant mechanical finishing.
Now that you’ve got your 3D-printed object, it’s time to follow through with the heat treatment process. But, how exactly do you do it so that the parts reach their fullest potential?
How to Successfully Heat-Treat 3D-Printed Parts
A leak-free vacuum furnace is the most important factor you need to consider for a successful additive manufacturing inert vacuum heat treatment. At most, the leak rate of your chamber must not go above 1 micron per hour, no matter what size it may be. This ensures that the materials will not undergo oxidation that may cause a negative—and possibly dangerous—reaction.
You also need to properly bake the vacuum chamber before starting any furnace cycle of 3D printing jobs. The recommended temperature is 2,400°F or 1316˚C at a minimum. However, temperature uniformity must be on top of mind as it is essential for heat-treating printed parts. If you do not follow this, it may result in scrap.
For example, a BJP-printed product may show a lack of temperature precision in the form of excess shrinkage or largeness. You need to ensure that it reaches the required temperature range of +/- 2°F.
Lastly, you need to keep the atmosphere of your vacuum atmosphere in pristine condition. 3D printing of any component is done to produce parts that are near-net-shaped. In other words, you’re creating pieces that don’t need much surface finishing as it is already near the ideal shape and size. However, surface contamination on printed titanium or nickel-based alloy may already be part scrap.
Quality 3D-Printed Parts with Vacuum Heat Treatments
3D printing is fast becoming a popular way of producing metal components as its cost-effectiveness optimizes the mechanical properties of the materials. From plastic materials to metallic powders, you can create anything using this technology.
However, keep in mind that vacuum heat treatment is an integral part of the 3D printing process. No matter what additive manufacturing method you deploy, heat-treating is a must to achieve the goal of crafting items that are very close to the end product’s final shape. And for this, you need a high-quality lab furnace specialized for this process.
To help you in your search, check out AI Furnace’s selection of lab furnaces today. We carry a range of lab furnaces, including high-temperature, controlled atmosphere, muffle furnaces, and more. If you need assistance with choosing a lab furnace that can support your vacuum heat treatment process, fill out our contact form and we’ll get in touch with you.